ABS Plastic: Understand the Key Benefits and Applications
Acrylonitrile Butadiene Styrene (ABS) plastic is a widely used thermoplastic polymer known for its versatility, durability, and ease of processing
ABS is popular in various industries and applications, including automotive parts, consumer goods, electronics, and toys. We offer ABS and ABS-like materials through the following services:
Advantages of ABS
- Impact resistance: ABS plastic is known for its excellent impact resistance, making it suitable for applications that require durability and toughness.
- Strength and stiffness: ABS has good mechanical properties, including high strength and stiffness. Its ability to withstand loads and stresses makes it suitable for structural components.
- Versatility: When it comes to manufacturability, ABS plastic is a versatile material that can be easily molded and shaped through various services, such as injection molding, machining and 3D printing.
- Chemical resistance: The material exhibits resistance to a wide range of chemicals, including acids, alkalis, and various solvents.
- Electrical insulation: ABS has good electrical insulating properties, so you will find it in electrical and electronic components, housings, and enclosures.
- Surface finish: ABS plastic can be easily finished and post-processed for a smooth and aesthetically appealing surface.
Disadvantages of ABS
- Poor weather resistance: The material is susceptible to degradation when exposed to sunlight and UV radiation. It can become brittle and discolored over time, limiting its outdoor applications.
- Flammability: ABS plastic is classified as a combustible material and has a relatively low resistance to fire. It tends to melt and burn, releasing potentially toxic fumes. Flame-retardant additives can be used to improve its fire resistance.
- Limited heat resistance: The material has a relatively low melting point, typically around 200-240°C (392-464°F). It may deform or lose its mechanical properties at higher temperatures, restricting its applications.
- Dimensional instability: ABS has a higher coefficient of thermal expansion compared to other engineering plastics. This can lead to dimensional changes with temperature variations, making tight tolerances challenging to maintain.
How are ABS Parts Manufactured?
ABS plastic parts can be produced using various manufacturing processes. The ideal production method is influenced by quantity needed, geometry, and the desired properties of your part. Some common methods include:
- Injection molding: Injection molding is the most common process used to manufacture ABS plastic parts. The service is suitable for producing high volumes of complex parts with precise dimensions and intricate details.
- CNC machining: The material can also be machined using computer numerical control (CNC) milling or turning machines. CNC machining is suitable for producing low-volume or customized ABS parts with tight tolerances.
- 3D printing: ABS plastic is a popular material for 3D printing, especially with FDM (Fused Deposition Modeling) 3D printers. There are also many ABS-like materials available for SLA 3D printing. This route allows for the production of complex geometries and prototypes with relatively low setup costs compared to traditional processes like injection molding.
- Extrusion: ABS can be extruded to create continuous profiles, such as tubes, rods, and sheets. The extruded ABS can be cut into specific lengths to produce parts.
- Blow molding: Blow molding is typically used for producing hollow ABS plastic parts, such as bottles, containers, and automotive components. The process involves inflating a molten ABS plastic tube inside a mold cavity, creating the desired shape as it cools and solidifies.
- Thermoforming: Thermoforming is a process used to produce ABS plastic parts from sheets. The ABS plastic sheet is heated until it becomes pliable, and then it is stretched over a mold and cooled to take on the desired shape. Thermoforming is commonly used for producing packaging, trays, and automotive interior components.
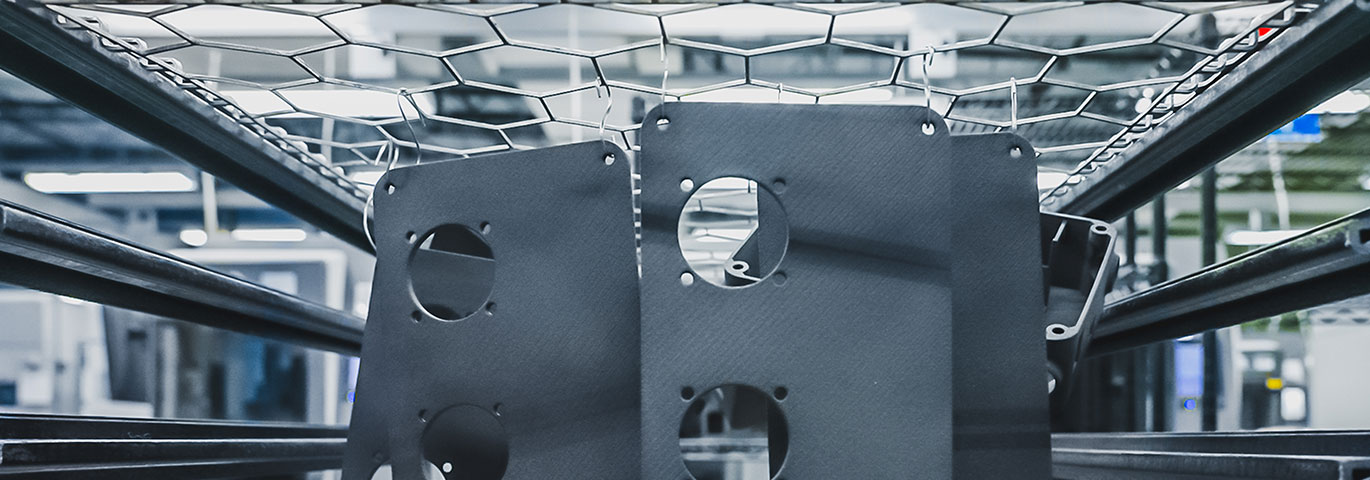
ABS-like plastics are commonly used in 3D printing along with finishing options to expand applications.

Applications of ABS
ABS plastic is used to produce a wide range of products across various industries. Some common industries and types of products made out of ABS plastic include:
- Consumer electronics: ABS plastic is commonly used in the production of consumer electronics such as computer keyboards, computer mouse, remote controls, phone cases, and audio/video equipment housings. Its impact resistance, versatility, and electrical insulation properties make it suitable for these applications.
- Automotive parts: The material is widely used in the automotive industry for various interior and exterior components. Examples include dashboards, instrument panels, door panels, trim, grilles, mirror housings, and interior console parts. ABS plastic's strength, impact resistance, and surface finish make it suitable for automotive applications.
- Toys and games: ABS plastic is a popular material for manufacturing toys and games due to its durability, impact resistance, and ability to be molded into intricate shapes.
- Household appliances: ABS plastic is used in the production of vacuum cleaners, blenders, coffee makers, toasters, and kitchen utensils. Its strength, chemical resistance, and ease of processing make it suitable for these applications.
- Medical devices and equipment: The material is used in the medical field for producing a range of devices and equipment. This includes medical instrument housings, equipment casings, laboratory equipment, disposable syringes, and medical device components. ABS plastic's durability, chemical resistance, and ease of sterilization make it suitable for medical applications.
- Sports and recreation equipment: ABS plastic is employed in the manufacturing of sports and recreation equipment such as helmets, protective gear, athletic equipment, skateboards, and bicycles. Its impact resistance and ability to withstand outdoor conditions make it suitable for these applications.
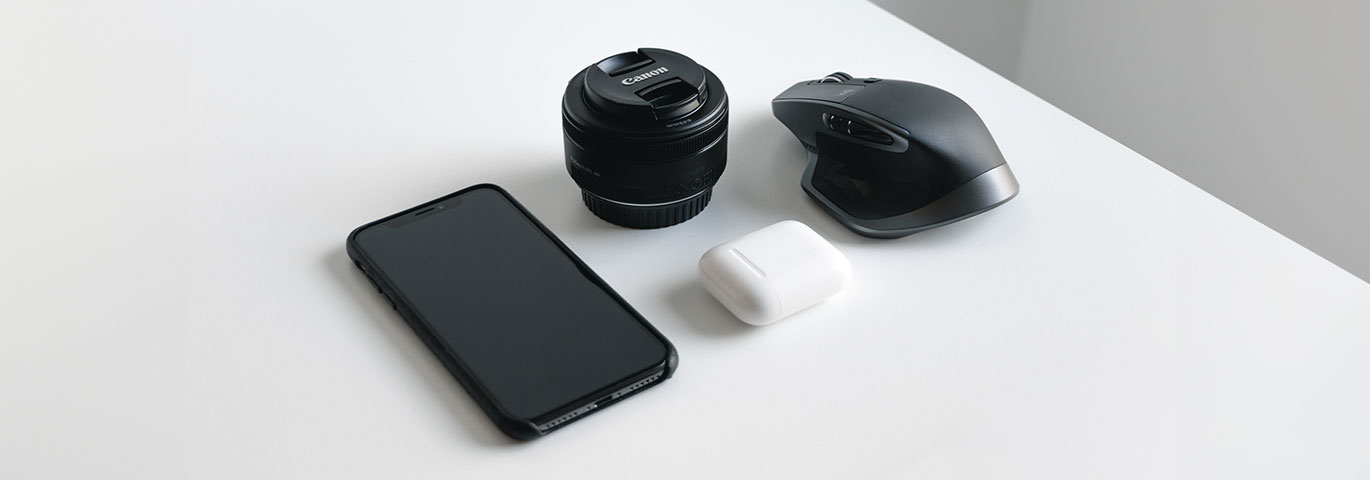
Thanks to its impact resistance and electrical insulation properties, ABS is a popular plastic for consumer electronics.
Plastic Materials Similar to ABS
There are several materials that are similar to ABS in terms of their properties and applications. Here's how they compare to ABS:
- Polystyrene (PS): Polystyrene shares some similarities with ABS in terms of its transparency, ease of processing, and affordability. However, it has lower impact resistance and mechanical strength compared to ABS. PS is commonly used for packaging materials, disposable cutlery, and insulation.
- Polypropylene (PP): Polypropylene is another thermoplastic that shares some similarities with ABS. It has good chemical resistance, high heat resistance, and low density. However, PP has lower impact strength and stiffness compared to ABS. PP is commonly used for automotive parts, packaging, containers, and household products.
- Polycarbonate (PC): Polycarbonate is a transparent thermoplastic known for its high impact resistance and excellent clarity. It has similar impact resistance to ABS, but PC is generally more expensive. It is commonly used in applications that require optical clarity, such as automotive lighting, safety goggles, and electronic display screens.
- Polyethylene (PE): Polyethylene is a versatile thermoplastic known for its excellent chemical resistance and low friction properties. It has lower impact strength and stiffness compared to ABS. PE is commonly used for packaging, pipes, containers, and various household products.
- Polyamide (Nylon): Nylon is a strong and durable thermoplastic with good mechanical properties. It has similar or higher impact strength compared to ABS but is more expensive. Nylon is commonly used in applications that require high strength and wear resistance, such as gears, bearings, and automotive parts.
More Resources