Nylon vs. Delrin: Strong, Durable Materials Ideal for High-Wear Applications
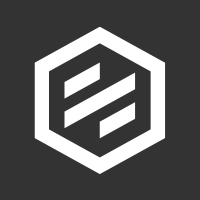

If you’re looking for materials that are built to last, look no further than nylon and Delrin, an acetal homopolymer. These two multipurpose materials offer durability, strength, and long-term wear resistance, and both are ideally suited for an array of injection molding and machining projects. Both nylon (polyamide) and Delrin (polyoxymethylene) have a low friction coefficient and are resistant to chemicals and UV light. However, depending on your specific application or the project requirements you have in mind, there are crucial differences between the two materials that could make one better suited to your precise needs.
The Benefits of Nylon
Nylon is an incredibly sturdy plastic that has high heat resistance and high temperature strength, which makes it an ideal choice for electrical applications and automotive components. There are many different types and multiple grades of molded nylon materials, each with their own distinctive qualities and unique properties that can suit the precise specifications of most projects and applications. Nylon is also an extremely compatible material to use with 3D printing, a desirable manufacturing option that Delrin lacks.
Molded Nylon Options
There are various molded nylon materials, each with its own set of advantages.
- Nylon 66: General purpose nylon which offers great hardness, stiffness, and abrasion It has a tensile strength of approximately 12,000 psi, a high melting point, and mold temperatures ranging from 100°-225°F (38°-107°C).
- Nylon 46: A heat-stabilized and RoHS compliant injection molding nylon with very high thermal deflection, melting temperature, and mold temperature.
- Filled Nylon: One of the strongest plastics available for the molding process. Has a high stiffness-to-weight ratio and strong mechanical properties.
- Mineral-filled Nylon: A 40% mineral-reinforced nylon 66 with a melting point of 505°F (263°C), >600 electrical CTI, and HB (self-extinguishing) flammability rating.
- Glass-filled Nylon: Offers high tensile strength and Rockwell hardness with extremely high melting points. Options include 13%, 14%, 15%, 20%, 33%, 35%.
These nylon options are all extremely durable materials, and they all possess high-temperature strength, especially when they are reinforced. All of these molded nylons offer high wear resistance and chemical resistance, except when exposed to strong acids and bases. Also, nylon is electrically nonconductive and insulative, making the material perfectly suited for electrical and automotive applications.
Typical Nylon Parts |
---|
|

3D Printing with Nylon
The benefit of using nylon with 3D printing is that customers have more freedom in their part designs and can introduce more complex geometries in their products, doing away with the limitations of more traditional manufacturing processes. There are multiple grades of nylon to choose from that can be used with either selective laser sintering (SLS) or Multi Jet Fusion (MJF) 3D printing processes.
Whichever grade of nylon you choose, these powdered thermoplastic materials forge strong, durable parts that possess mechanical properties that are perfectly suitable for both functional prototyping and end-use projects. 3D-printed nylon is extremely durable, has high heat resistance, and terrific long-term wear resistance.
Here’s a list of various grades of nylon and their accompanying benefits, followed by charts comparing their properties:
- PA 12 White (PA 650): Good general purpose nylon and a cost-effective material choice, with good strength and stiffness.
- PA 11 Black (PA 850): Has the highest elongation at break of all additively manufactured nylons, and the best ductility of nylons. Has a uniform deep-black color that provides a clean look and showcases its features.
- PA 12 Black: An economical material choice, with nearly isotropic mechanical properties.
- PA 12 Mineral-filled (PA620-MF): Has the highest stiffness of all additively manufactured nylons, with high temperature resistance and is tops among nylon materials for heat deflection.
- PA 12 40% Glass-filled (PA614-GS): Has the highest stiffness of all additively manufactured nylons, with high temperature resistance and long-term wear resistance.
- PA 12 40% Glass-filled Black: An economical choice, with high heat deflection and great dimensional stability.
What is Delrin Material Used For?
Delrin acetal homopolymer is an ideal material for a range of industrial and mechanical applications, and it is one of the most popular plastics used for injection molding and CNC machining projects. Delrin is an excellent alternative to metal due to its:
- High density
- Resilient surface
- High tensile strength
- Long-term resistance to wear
- Low friction coefficient
- Prolonged durability
- Overall toughness
Delrin also has excellent machinability, high precision, good dimensional stability, superior impact capability, high fatigue endurance, and terrific wear and abrasion properties, making it a desirable material for parts that will encounter heavy wear over time.
Typical Delrin Parts |
---|
|
In wet environments, Delrin really shines due its extremely low moisture absorption rate, high performance, and dimension retention. This makes it the perfect choice for pump and valve components. Delrin is a highly versatile material, with superior density and substantial creep and wear resistance. It is also chemically resistant to hydrocarbons, solvents, and neutral chemicals. Delrin’s natural grade is FDA, NSF, and USDA compliant, to ease any concerns about using the material in any suitable situation. One drawback to Delrin is it is not ideal for use with 3D printing, and for those applications, nylon would be a highly suitable substitute.
For points of reference, here are some vital statistics in key categories for Delrin:
Material | Tensile Strength | Impact Strength | Heat Deflection | Elongation at Break |
Delrin | 6,000 - 22,000 psi | 0.75-2ft-lb/in. | 180-300 °F | 10-40% |
Delrin comes in two forms: Delrin 150 and Delrin 570 and each has distinctly different properties and specifications.
Nylon and Delrin: The Bottom Line
Both nylon and Delrin are strong, durable materials that can be used for a variety of industrial, mechanical, electrical, and automotive applications. They are versatile materials that are resistant to abrasion, heat, long-term wear, and high impact. Best of all, with multiple grades and types of nylon and Delrin to choose from, you’re likely to find one that will suit the specific requirements of any application or project.
|
Abrasion resistance |
Low friction |
Complex geometries? |
Moisture resistance |
High temp tolerance |
3D printing |
Machinability |
Wear resistance |
Nylon |
✔ |
✔ |
✔ |
|
✔ |
✔ |
|
|
Delrin |
|
✔ |
|
✔ |
|
|
✔ |
✔ |
Nylon is the best material to work with if you are looking to use 3D printing capabilities, and it also can be used in higher temperature situations than Delrin. Delrin has the edge in applications that require lower moisture absorption in damp, wet environments, and Delrin also works extremely well as a material for machined parts.
No matter what material you decide to work with, both nylon and Delrin are tough, long-lasting plastics that will perfectly suit whatever application or project you can dream up.