Design Guidelines: CNC Milling
Our basic guidelines for CNC milling include important design considerations to help improve part manufacturability, enhance cosmetic appearance, and reduce overall production time.
Size
Maximum Dimensions (3-axis milling)
10 in. x 7 in. x 3.75 in. |
10 in. x 14 in. x 1.75 in.* |
22 in. x 14 in. x 0.75 in.* |
22 in. x 14 in. x 3.75 in.** |
254mm x 177.8mm x 95.25mm |
254mm x 356mm x 44mm* |
559mm x 356mm x 19mm* |
559mm x 356mm x 95.25mm** |
Maximum Dimensions (5-axis milling)
2.6 in. x 2.9 in. x 3.9 in. |
66mm x 73mm x 99mm |
Minimum Dimensions
SIZE | 0.25 in. x 0.25 in. |
---|---|
NOMINAL THICKNESS |
0.040 in. |
SIZE | 6.35mm x 6.35mm |
---|---|
NOMINAL THICKNESS |
1.02mm |
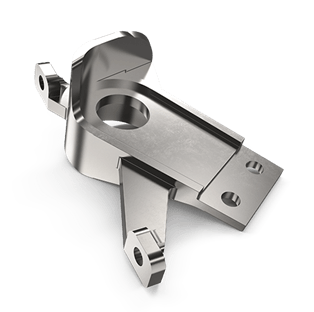
Typically, Protolabs can hold a machining tolerance of +/- 0.005 in. (0.13mm). Part features are recommended to be thicker than 0.020 in. (0.51mm) in all regions and a nominal part thickness above 0.040 in. (1.02mm) is required. Maximum depth that can be milled is 2 in. (50.8mm) from either side of part. For specific milling dimensions by material, see maximum part extents for machining.
*These part sizes can only be milled from two sides, and in ABS, acetal, and aluminum 6061 and 7075.
**This part size can only be milled from two sides, and in Aluminum 6061 and 7075.
Advanced CNC Milling Capabilities
Production Parts
Reduce your CNC machining costs when you order higher quantities of machined parts. Our production capabilities for machining—powered by our New Hampshire-based facility, Rapid Manufacturing—allow up to 1,000+ machined parts along with first article inspection (FAI) reporting, material certifications, part assembly, and additional finishing options like anodizing and chromate plating. Learn more about your production options for machining.
5-Axis Milling
We use 5-axis indexed milling—in addition to 3-axis milling and turning—to machine parts. 5-axis indexed milling (also referred to as 3+2 milling) allows for more complex geometries and non-orthogonal features like off-axis holes. Better finishes are also possible on non-orthogonal surfaces and because 5-axis milling increases machining efficiencies, more cost-efficient parts can be had. Read about designing complete features on machined parts.
CNC Machining Surface Finish Guide
Get a realistic snapshot of the surface finishes that are possible on machined plastic and metal parts.
DOWNLOAD >
Design Essentials for CNC Machining
We've compiled some of our best design tips to help you optimize your part design for CNC machining.
DOWNLOAD >
Materials
|

Anodizing and Chromate Plating
Add these specialized finishes to your order to extend the life and improve the look of your parts.
Anodizing
Reduce corrosion and add an appealing metallic coloring to your aluminum parts. Anodizing helps resist scratching, acts as an electrical insulator, and is one of the most durable finishes available.
Specifications:
- Type II
- ROHS compliant
- Class 1 (clear)
- Class 2 (black)
Chromate Plating
Protect your parts from corrosion while adding electrical conductivity and the ability to paint your part. Note that steel and iron-based metals require pretreating with zinc before applying chromate.
Specifications:
- Type I, Non-ROHS (yellow)
- Type II, ROHS (clear)
- Class 1A: For maximum protection against corrosion, painted or unpainted
- Class 3: For maximum protection against corrosion where low electrical resistance is required
Surface Finishes
Typically, we break (debur) the edges on all machined parts. All machined plastic parts are left as-machined, which may leave visible tool marks. Some metal parts, on the other hand, allow more choice. Parts left with sharp edges should be handled with care.
PLASTIC |
Edges broken with visible toolmarks |
---|---|
ALUMINUM |
Edges broken with visible toolmarks, edges broken with light bead blast, or sharp edges with visible toolmarks |
ALL OTHER METALS |
Edges broken with visible toolmarks or edges broken with light bead blast |

Threaded Holes
We currently support UNC and UNF threads from #2 up to 0.5 in., and metric threads from M2 to M12. Avoid modeling internal threads on your part design.
VIEW THREADED HOLES GUIDELINES >
Radii
Sharp inside corners on a part will be radiused (rounded) as a natural result of the CNC machining process. Resulting radii will be identified on your quote.
Text
Recommended text considerations for CNC milling:
- Plastic and soft metals: Minimum width of 0.018 in. (0.457mm), depth of 0.0118 in. (0.3mm). Example text size would be 16 point Arial Rounded MT font.
- Hard metals: Minimum width of 0.033 in. (0.838mm) and depth of 0.0118 in. (0.3mm). Example text size would be 22 point Arial Rounded MT font.
- If design permits it, opt for recessed text versus raised.
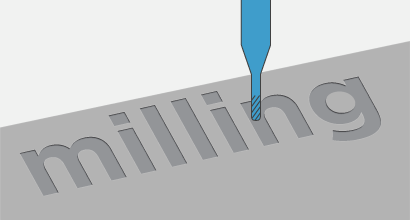