In the 32-year history of additive manufacturing (AM) and 3D printing—terms used interchangeably—many myths, misconceptions, and untruths have been shared in writing, at events, and in conversations. The following are among those that people continue to share and believe.
1. Additive Manufacturing is a "Push Button" Process
Some of you, and hopefully many, know that this is the furthest from the truth. Those less familiar may see AM as magic. Click start, go to lunch, and return to a finished product. Building high-quality polymer parts can take a lot of work, and metal parts can require significantly more. Much of the work can be in removing support material. Even more can involve finishing the surface, depending on what is required, and the solution used.
Building good AM parts starts with good design. Build orientation and nesting multiple parts in the build volume are also key. Both can have a considerable impact on the build time, where support material may be attached, and surface quality. Planning is key, but it can occur only after one has sufficient knowledge and experience so that the best decisions are made when designing and preparing parts for AM.

2. Additive Manufacturing Systems Produce Ready-to-Use Parts and Complete Products
This is the exception and not the rule. In other words, most parts made by AM require the removal of support material, finishing of the surface, and painting or adding a clear coat, in the case of polymer parts—all services available from Protolabs. While this is true most of the time, clips, brackets, and some other types of parts made in polymer require little post-processing time and effort. With the exception of cooling, and cleaning loose powder from them—in the case of powder bed fusion (PBF)—they are ready to use with little post-processing.
Metal parts can require many post-processing steps, which can increase time and cost. Depending on the application and specific requirements, metal parts made by PBF can involve: 1) removal of excess powder and safely transferring it to another location, 2) thermal stress relief to reduce the possibility of warping, 3) cutting parts from the build plate using wire EDM or a band saw, 4) hot isostatic pressing to eliminate porosity in the parts, 5) removal of support structures used to anchor the part and its features to the build plate, 6) additional heat treatment, 7) surface treatment such as shot peening and CNC machining, and 8) inspection and quality assurance.
Most often, AM is used to produce an element of a product rather than an entire, completely functional product. Consider eyewear, footwear, and sporting goods, as well as parts for aircraft, automobiles, and machines. Parts made by AM contribute greatly to the product, but many other parts are made conventionally and assembled.

3. Additive Manufacturing is Fast and Inexpensive
When building relatively small parts in low volumes, AM can be fast and cost-effective. AM reduces or eliminates the need for tooling, such as molds and dies, which can contribute to lead times and cost. With AM, it is possible to produce the first few, or even hundreds of parts, faster and less expensively than with conventional methods of manufacturing. When considering complexity that can be designed into a part, AM can be a good choice. Material options are also a big part of the decision-making process.
When compared to high volumes of parts made by injection molding and other forms of manufacturing, AM can be far slower and more expensive. Consider a part the size of a baseball in a quantity of 50,000. In most cases, conventional manufacturing would be the best option in both speed and cost. If the part is much smaller and the quantity is much lower, AM may be the best method of production. When producing parts with molds and dies, you are locked into that design. Changes are possible, but they delay production and can be expensive. With AM, you can produce a part one day, make design changes as necessary, and return to production the following day. Also, it is possible to mix designs in the same production batch of parts. In the end, a decision on whether to use AM based on speed and cost depends on many factors.
4. Additive Manufacturing Systems are Similar
AM systems are almost as wide-ranging as conventional methods of manufacturing. Nearly all systems build parts layer by layer, but that is where most similarities end. AM machines range in price from about $200 to several millions of dollars. Build volumes range from a few centimeters to many meters in size. Also wide-ranging are the specific processes used, energy sources, and the types of materials and the forms in which they are delivered. Materials for AM can be powders, liquids, filaments, wires, pellets, or sheets, depending on the process.
The ISO/ASTM 52900 terminology standard defines seven distinct AM processes as outlined in the following. They reflect the diversity of systems and materials they accept.
- Material extrusion—an AM process in which material is selectively dispensed through a nozzle or orifice
- Material jetting—an AM process in which droplets of build material are selectively deposited
- Binder jetting—an AM process in which a liquid bonding agent is selectively deposited to join powder materials
- Sheet lamination—an AM process in which sheets of material are bonded to form a part
- Vat photopolymerization—an AM process in which liquid photopolymer in a vat is selectively cured by light-activated polymerization
- Powder bed fusion—an AM process in which thermal energy selectively fuses regions of a powder bed
- Directed energy deposition—an AM process in which focused thermal energy is used to fuse materials by melting as they are being deposited

5. Parts Are Not as Good as Those Made with Conventional Methods
This can be the case, depending on many factors. For example, if a part is produced on a low-cost, desktop machine, chances are reasonable that it will not match the aesthetic quality and mechanical strength properties of a molded plastic part.
Countless organizations around the world use AM to produce parts that are currently in service on aircraft, satellites, automobiles, and industrial machines. Millions of AM parts have been made for medical products, sporting goods, eyewear, and footwear. All of them meet or exceed the requirements of these industries and applications. This illustrates that AM parts can be as good, and sometimes even better, than parts made using conventional methods of manufacturing.
6. Complexity is Free
For years, many have said that AM offers complexity for free. The actual production process does not care much about complexity, but other elements of the start-to-finish process do. For example, it takes more time, talent, and effort to create a complex design compared to a simple one, which adds cost to the product. Removing support material, finishing the surface, and inspecting complex AM parts can be more difficult and costly.
Producing a complex product that only AM machines can build comes with many potential benefits. For example, it may be possible to consolidate many parts into one, digitally, and then build it. This can eliminate part numbers, manufacturing processes, inventory, assembly labor, maintenance, and inspection. Using topology optimization can reduce material and weight and often results in a shape that can only be produced affordably on an AM system. The use lattice and mesh structures can further reduce weight and improve product performance—structures made possible by AM.

7. Few Materials are Available
This was the case years ago, but far more materials are available today. Many hundreds of AM material options have been commercialized. As examples, companies have recently introduced copper for metal powder bed fusion, photopolymers for Carbon’s process, implant-grade PEEK in filament form, and polypropylene for laser sintering and HP Multi Jet Fusion. Even so, far fewer materials are available, compared to the thousands of materials for conventional methods of manufacturing.
8. Most AM Inventions Occurred Years Ago
With the AM industry 32 years of age, one might assume that most inventions related to AM occurred many years ago. Far more have occurred in recent years than in the industry’s first 25 years, combined. To illustrate, Wohlers Report 2020 includes information on more than 200 manufacturers of industrial AM systems that were produced and sold machines last year. Not all include original IP, but many do.
9. Most Homes Will Have AM in the Future
In the 2012–2013 time frame, a lot was published and said about how 3D printers would be in every home, turning out products as an alternative to buying them elsewhere. Wohlers Associates has never bought into this notion, then and now. Making decent parts on machines at home requires skill and experience. Suppose you have the skill, talent, and software, but does your 3D printer offer the correct material or size required for the product? Producing desired aesthetics and surface finish are also considerations that many people underestimate.
10. AM Systems Print Human Organs
This may be one of the biggest myths of all. Some early samples have been produced, but it is still very much in research and development. Vascularization remains a challenge. Perhaps someday, hopefully in your lifetime, it will be possible to order a patient-specific heart, kidney, or liver produced from cells taken from the patient’s body and 3D printed. Those close to the process claim it is still many years away.
Many myths associated with AM have developed over the years, even among some sources trusted as authorities. This only exacerbates the confusion. As a rule, validate what you read or hear. Those who share information may have good intentions, but they sometimes get it wrong.
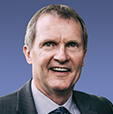
Terry Wohlers is principal consultant and president of Wohlers Associates, Inc., an independent consulting firm he founded 33 years ago. Through Wohlers Associates, he has provided consulting assistance to more than 275 organizations in 27 countries, as well as to 180+ companies in the investment community. He has authored 425 books, articles, and technical papers and has given 160 keynote presentations on six continents. Wohlers served as a featured speaker in events held at the White House in 2012 and 2014. He has appeared on many television and radio news programs, including Bloomberg TV, CNBC, CNN, Fox Business, MSNBC, NPR, and Australia’s Sky News. Wohlers is a principal author of the Wohlers Report, the undisputed industry-leading report on additive manufacturing and 3D printing worldwide for 25 consecutive years. DOWNLOAD REPORT.