Key Considerations Before Choosing Multi-Cavity Injection Molding
By Michael Adams, Applications Engineer, Protolabs
Injection molding continues to be one of the most commonly used manufacturing processes in the world for plastic parts because of its efficiency, consistency, and cost-effectiveness.
Injection molding for custom parts works well for a variety of industries, such as automotive, aerospace, medical devices and medtech, construction, consumer electronics, and more. Digital manufacturers can provide custom injection molding for plastic prototypes and on-demand production parts in days. For greater efficiency, multi-cavity molding is a popular choice for customers.
What is Multi-Cavity Injection Molding?
The typical pathway for injection-molded parts is a single-mold method—offering one cavity to build one part at a time. However, in some cases, there is an option to use multi-cavity molding, a process that enables the production of multiple versions of the same part in a single shot (one injection molding cycle).
In other words, multi-cavity molding is a tool designed to produce multiples of the same parts, enabling the efficiency of turning out two, four, and eight parts at a time. Multi-cavity molds often come into play for mass production of parts, but we're also finding the method sometimes can be suitable for lower volume production.
Before opting to use multi-cavity molding, we recommend that you consider several issues:
- Whether to use multi-cavity molding in the first place from a design, quantity, and pricing standpoint
- How part complexity and geometry determine whether this molding method can be used
- How a part's lifecycle development can be affected

Why use Multi-Cavity Injection Molding?
Essentially, the two primary reasons to choose multi-cavity molds to produce parts are for meeting quantity/demand needs, and for reducing piece-part price.
Generally speaking, engineers and product designers are not as concerned abut pricing or cost. Their focus is to validate their part designs at lower quantities. That said, procurement managers are concerned about price, especially piece-part price, so this issue should be given careful consideration.
There also is a general notion that reducing piece-part price for a project means initially having a higher mold or tool price but a lower piece-part price, depending on quantities. But that's not always true. Having more cavities doesn't necessarily equate with cost-effectiveness. The cost depends on several variables, such as the price of the tool (mold) and the cost of the part. These don't always, if you will, "crossover".
Understand Cost with Protolabs' Digital Quoting System
Protolabs' digital quoting system features a value-pricing calculator. Using it helps you determine overall costs, so you can see where the equilibrium or "crossover" would occur between a possible higher tool price, but, eventually, depending on quantity, a lower piece-part price.
Upload A Part
Consider Part Complexity
Not every part design lends itself to multi-cavity molding. This decision depends largely on a part's complexity and geometry. For the most part, basic guidelines still apply for multi-cavity molding, but there are some design differences to consider. Engineers and designers should look carefully at gating considerations, side actions, and pick-outs:
Gating
Gates in injection molding allow molten plastic to flow into the mold at the beginning of the injection cycle and then hold it under pressure until the mold cools, the plastic has solidified, and the part is subsequently ejected.
In mold-making, there are many different types of gates. We typically rely on pin-style and hot-tip gates, which are often used on single-cavity molds to solve challenges with complex part geometries and to reduce gate vestige—the small remnant of runner material that must be trimmed from the finished workpiece. However, there are no direct gating options in multi-cavity molding—a tab or runner system must be used.
Side Actions and Pick-Outs
These design elements, which can work well for single-cavity molding, don't always apply to multi-cavity tools, or if they do, they may not be very efficient. Case in point: manually loaded pick-outs—for example, placing a small block of metal into a mold cavity to create a cutout on an internal feature—are straightforward in a single-cavity tool. That same approach on an eight-cavity tool, however, is time-consuming, and should be avoided if large quantities are in your product's future.
Beyond these specific design elements, customers also sometimes ask us about family molds. Basically, family molds can be an option purely for pricing reasons. Additionally, much like multi-cavity tools, part complexity and geometry will dictate whether a family mold can be an option. The difference in these processes? Multi-cavity molding describes a tool with cavities designed to produce multiples of the same part. Family molding describes a tool with various cavity designs such as left and right components that can then mate together.
Collaborating with an applications engineer first before investing in multi-cavity molds is recommended. As stated in this section, though basic design guidelines are generally the same, there are some important differences to consider. Also, it should be noted, Protolabs will refund the price of the stand-alone, single-cavity mold when a customer invests in multi-cavity molds.
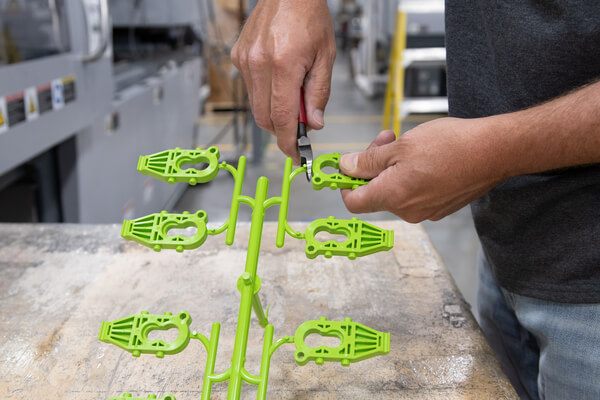
Industry Uses for Multi-Cavity Molding
Examples of industry applications for multi-cavity molding abound. Automotive OEMs use the tooling for high-volume fasteners, connectors, sub-assembly components, interior trim sets, ad small standard parts. The construction sector uses the tooling for commodity items like fittings, fasteners, connectors, and closures. Consumer electronics applications include housings, and internal components for specific devices. Medtech and medical device industry applications include disposable items and casings for handheld diagnostic tools or kits. The list goes on.
In the end, consider multi-cavity molding if the option makes sense in the context of the quantity/demand, piece-part pricing, mass production, and low-volume production considerations. As aways, feel free to discuss your design needs with a Protolabs applications engineer, at 877-479-3680 or customerservice@protolabs.com.
Michael Adams has been an applications engineer at Protolabs since 2016. He specializes in injection molding and CNC machining, including insert molding and overmolding. Adams has designed plastic parts and molds for more than 30 years, with experience that includes rotational molding, blowmolding, thermoforming, extrusion, and long-fiber composite pultrusion.