
Insert Molding Service
Get custom plastic parts molded with metal inserts. Upload a part to get an online quote.
Certifications ISO 9001:2015 | CTQ Inspections | ITAR
ISO 13485 certification available through Protolabs Network
Our insert molding processes produce custom prototypes and on-demand production parts in as fast as 15 days. We use aluminum molds that offer cost-efficient tooling, producing parts from a range of thermoplastic and liquid silicone rubber materials.
Insert molding is frequently used for:
- low-volume production parts
- bridge tooling
- pilot runs
- functional prototyping and testing

Insert Molding Design Guidelines
Our basic guidelines for insert molding include important design considerations to help improve part manufacturability, enhance cosmetic appearance, and reduce overall production time. View our design guidelines page for more in-depth details.
US | Metric | ||
Maximum Part Size | 18.9 in. x 29.6 in. x 8 in. | 480mm x 751.8mm x 203.2mm | |
Volume | 59 cu. in. | 966,837 cu. mm | |
Depth | 4 in. from parting line | 101mm from parting line | |
up to 8 in. if the parting line can pass through middle of part | Up to 203.2mm if the parting line can pass through middle of part | ||
Projected Mold Area | 175 sq in. (plastic) | 112,903 sq. mm (plastic) | |
48 sq. in. (silicone rubber) | 30,958 sq. mm (silicone rubber) |
Additional Notes
- Minimum part volume is 0.025 cu. in. (40.98 cu. mm).
- With substrate molds, we can maintain a machining tolerance of ±0.003 in. (0.08mm) with an included resin tolerance that can be greater but no less than 0.002 in./in. (0.002mm/mm).
- With thermoplastic overmolds, tolerances remain the same as substrate molds, however, if the overmold is LSR, then tolerances shift to 0.025 in./in. (0.025mm).
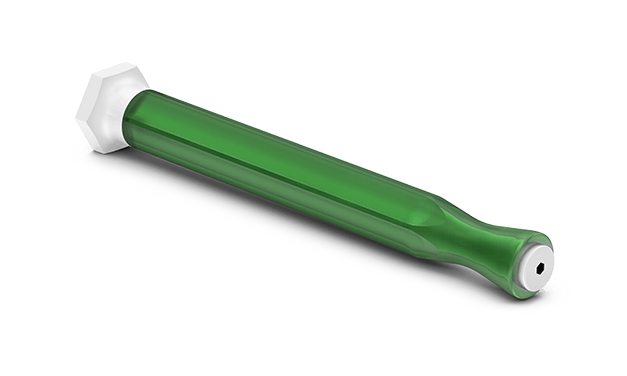
Instead of a mold that produces a final part using two separate shots like overmolding, insert molding generally consists of a preformed part—often metal—that is loaded into a mold, where it is then overmolded with plastic to create a part with improved functional or mechanical properties. We currently accept inserts from PEM, Dodge, Tri-Star, Spirol, and Tappex. A complete chart of stocked inserts at Protolabs is available here.
One way insert molding is used is with threaded inserts, which reinforce the mechanical properties of plastic parts’ ability to be fastened together, especially over repeated assembly. Bushings and sleeves are another great way to increase part durability for mating components that need more abrasion resistance due to moving parts.
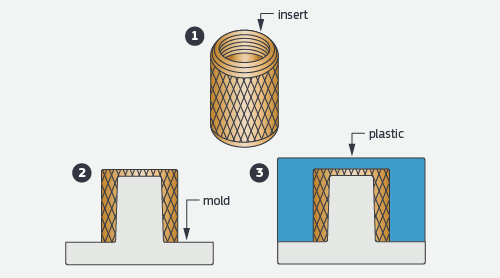