Multi-Cavity and Family Injection Molding
Maximize each shot with multiples of the same or different parts from a single mold
What is Family and Multi-Cavity Molding?
Family molding and multi-cavity molding are techniques used to produce multiple parts from a single mold. Rather than producing a single part with each cycle, multiple parts can be produced with a single shot. Multi-cavity molding describes a tool with the same cavity designed to produce multiples of the same parts. While family molding describes a tool with various cavity designs such as a left and right components that mate together.

Family and Multi-Cavity Molding Capabilities
Our basic guidelines for multi-cavity and family injection molding include important design considerations to help improve part moldability, enhance cosmetic appearance, and reduce overall production time.
Tolerances: Typically, Protolabs can maintain a machining tolerance of +/- 0.003 in. (0.08mm) with an included resin tolerance that can be greater than but no less than +/- 0.002 in./in. (0.002mm/mm).
Injection Molding Materials
|
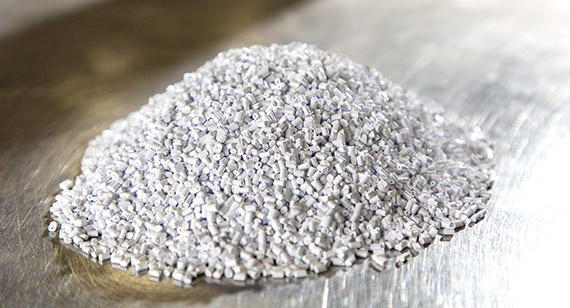

Surface Finish Options
Finish | Description |
---|---|
PM-F0 | non-cosmetic, finish to Protolabs' discretion |
PM-F1 | low-cosmetic, most toolmarks removed |
PM-F2 | non-cosmetic, EDM permissible |
SPI-C1 | 600 grit stone |
PM-T1 | SPI-C1 + light bead blast |
PM-T2 | SPI-C1 + medium bead blast |
SPI-B1 | 600 grit paper |
SPI-A2 | grade #2 diamond buff |
How Does Multi-Cavity or Family Molding Work?
Multi-cavity molds enable the production of multiple versions of the same part in a single shot. You can take this process to the next logical step when you include many different parts on the same mold, creating a family mold. If you have ever built a plastic model, you’ve probably worked with parts made in a family mold. The runners between each part are left intact, forcing you to break each part off the whole.
The advantages to these techniques are simple:
- High Production Volume: Significantly increases the number of parts produced per hour compared to a single-cavity mold
- Efficiency: Maximizes machine utilization
- Lower Per-part Cost: While the mold itself is more expensive initially, the cost per individual part drops dramatically due to the increased output rate and reduced cycle time per part
With this sort of intricacy, come challenges:
- Mold Complexity and Cost: It costs more to design and build a balanced multi-cavity mold due to the added complexity and time it takes to cut the mold, but you might make up for that with a lower piece-part price
- Balancing: Ensure that all cavities fill evenly and at the same rate for consistent part quality. Careful runner system design is critical
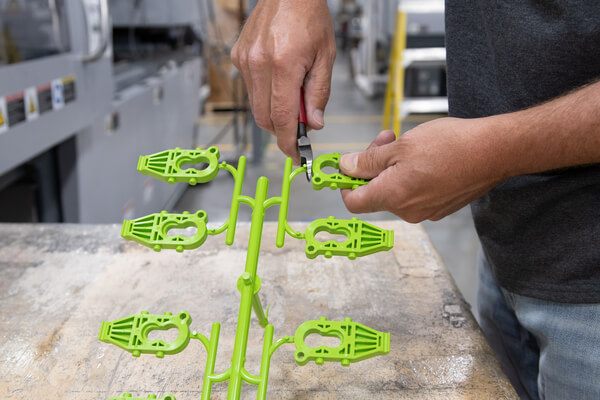
Automotive For high-volume fasteners, connectors, sub-assembly components, interior trim sets, and small standard parts |
Construction Commodity items like fittings, fasteners, connectors, and closures
|
Consumer Electronics Standardized components used across many units, housings, and internal components for specific devices |
Medical Devices Particularly for disposable items and casings for handheld diagnostic tools or kits |
Packaging Especially beverage, food, cosmetic, and pharmaceutical packaging
|
Appliances Housings and components for smaller appliances
|
Types of Parts | Function |
---|---|
Electronic device housings | Front/back casings, battery doors, button sets for a specific remote control, phone, or gadget |
Buttons and keys | Keyboards, control panels, remote controls |
Caps and closures | Bottle caps, jar lids, flip-tops, spray nozzle components (huge volumes needed) |
Connectors | Electrical connectors, terminal housings, fiber optic connectors (standardized, high quantity) |
Fasteners | Plastic clips, rivets, screw anchors, cable ties (commodity, high volume) |
Medical disposables and casings | Syringe barrels/plungers, pipette tips, test tubes, vial caps, parts for IV sets, sample cups. Two halves of a glucose meter casing, parts for a specific diagnostic test kit (high volume, consistency crucial) |
Small ears, bushings, washers | Standardized mechanical components |
Small pipe fittings | Elbows, T-connectors, caps for plumbing/irrigation |